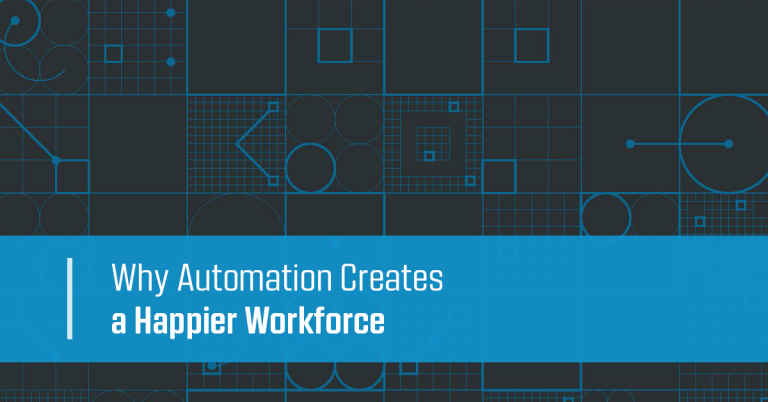
There are some long-held beliefs about the role automation will play in human society. These ideas have been perpetuated by sci-fi movies and books, by fearful workers considering how they need to keep their jobs to survive, and even by rock parody groups like Flight of the Conchords (The Humans are Dead).
Even if you don’t believe that robots will eventually gain sentience and unite to destroy their human oppressors, you might wonder: What happens to human workers if we automate essential positions within the manual labor force?
Automation in the supply chain will eventually reduce manual labor roles for humans. Right?
Wrong.
Plus One Robotics and Interact Analysis undertook a study based on the oft-cited “wisdom” that as repetitive warehouse roles are automated, human workers will be displaced; and the results were surprising.
A key finding in the Plus One Robotics and Interact Analysis white paper was this: Automation actually CREATES jobs. Though it seems counterintuitive, we found that more advanced warehouse automation results in quicker and more efficient eCommerce fulfillment, leading to greater demand for online orders and thus greater demand for warehousing. Though automation will displace some manual warehouse jobs, it will, for the foreseeable future, certainly create more manual jobs than it eliminates.
In fact, not only has automation been shown to improve efficiency and drive demand, thus creating more warehouse positions overall, but when we automate the rote and repetitive functions of picking, depalletizing, and conveyor induction, it creates opportunities for workers to step into more mentally stimulating (and often less physically demanding) jobs within the warehouse and supply chain infrastructure.
One example of this is PickOne, the software we create to provide robots with vision. PickOne learns over time, eventually reaching accuracy levels of 99 percent when picking items to pack. But it reaches that impressive level because we believe it is imperative to keep humans in the loop.
Yonder is the original “Human-In-The-Loop” remote supervisor software suite for robotic applications, and it runs with the help of human Crew Chiefs who act as managers to the many robots doing the manual labor. The Crew Chiefs help deal with exceptions that historically have derailed automated solutions and slowed warehouse operations down. Gone are the days of having a dedicated single on-site employee to handle a single mundane and repetitive task. We provide the future: a force multiplier where one remote worker handles several tasks at once.
Workers who previously performed repetitive and often dangerous tasks are freed by automation to upskill into other areas within the warehouse that may be more mentally challenging and fulfilling. In any industry, enjoying work and believing you make an impact is the key to employee engagement. Engaged workforces see lower rates of turnover--something critical to the warehouse and supply chain space where labor shortages and soaring rates of turnover have been ongoing issues.
Happy Employees are Productive Employees
Research from a team at Goldsmiths, the University of London quoted in a 2019 Financial Times article illuminated the lucky intersection of happy workers and productivity, noting that human-friendly companies (using automation for manual and rote tasks) often had more productive workforces, increasing efficiency and output overall.
There is a wealth of information available demonstrating that automation, which we’ve long known could improve efficiencies in the warehouse and supply chain environments, can also improve productivity, job satisfaction, and employee retention rates.
Download our white paper today and learn more about:
- Which warehouse jobs will see an increase as more warehouses automate
- How to increase throughput and efficiency without investment in additional labor or square footage
- Which jobs can be automated quickly for the least downtime and the greatest ROI
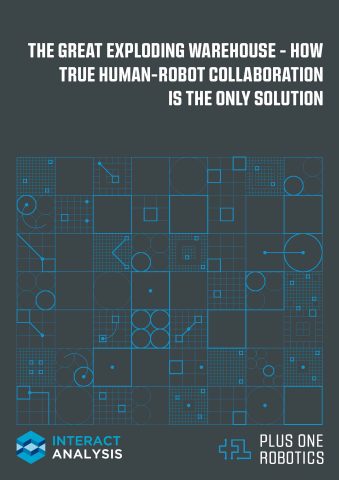