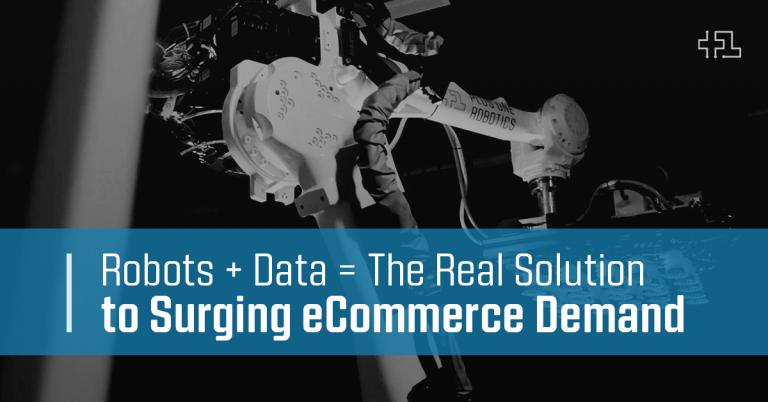
Analytics from Yonder, Plus One’s cloud-operated remote robot supervision and monitoring application, are setting the standard for automation data tools
Automation brings efficiencies to the warehouse, and in an era when ecommerce fulfillment demands are surging and customers expect shorter delivery windows, maintaining efficiency is a requirement for survival. Labor and warehouse space are at a premium, so increasing capacity in existing operations is top of mind for managers. Robots help, but it’s the data that comes with them that is the real value add. For Plus One Robotics’ Yonder dashboard customers, that critical data has provided key insights that reach far beyond the tasks they’ve automated to improve overall operational efficiency.
Anyone running a warehouse or fulfillment center understands that there are plenty of moving parts contributing to the entire operation's success. What logistics managers don’t always know is which pieces of their operation ultimately have the power to amplify ROI. Or they may think they’re running at peak levels when in truth, they could be missing their optimal throughput by a lot.
The robots will save us. (But not on their own.)
A customer recently implemented depalletizing robots to replace the workers unloading pallets at the warehouse in an effort to improve throughput. The depalletizing workers took on more value-added positions in the warehouse, such as that of Crew Chief. With enhanced analytics in place, the customer could see that both the robots and the human workers were underutilized. The dashboard made it clear that availability wasn’t the problem, which allowed the manager to look elsewhere to increase his throughput.
It’s not a leap to surmise that automation can be exceedingly helpful in seeing precise information and patterns to inform the control of specific aspects of warehouse operations. Complete with cameras and sensors, every robot is a data point.
People must self-report or be held to key performance indicators (KPIs) that might need adjustment at various points, while your robots will hit KPIs based on the way you spec them out. Every time. Instead of managing many people, who suffer from the variabilities that go hand in hand with being human, you’re now managing one or more robots. Problem solved, right? Maybe not. Or not entirely.
The robots are just one part of the solution to the warehouse optimization challenge. Robots do what they’re programmed to do. People must make sure that the programming makes sense in the larger context.
Metrics matter
We created Yonder, our remote supervision and monitoring software, to allow humans to remain in the loop as robots work. The Crew Chief can manage many robots remotely to handle exceptions and ensure availability as scheduled. Now we’ve built an enhanced dashboard in Yonder that provides powerful insights and analytics that bring greater value to logistics managers in the context of overall warehouse management.
Yonder’s enhanced dashboard is currently in beta, and we are finding that giving managers an overall view of performance is highlighting issues they didn’t know they had. Moreover, it is allowing them to optimize operations in areas outside of the automation they’ve implemented. The global dashboard uses the three key metrics all production facilities watch, thanks to the standardization of PackML (packaging machine language) and overall equipment effectiveness (OEE). These are availability, performance, and quality. These three metrics are powerful when we can examine how they interact and how they affect the performance of the operation overall.
How granular insights help customers manage capacity
In one operation, several robot teams were working on parallel lines in the warehouse. Before implementing the Yonder dashboard, it was clear that production wasn’t reaching capacity, but it wasn’t clear why. Once the dashboard broke down productivity into multiple teams, it was obvious that one team was outperforming the others, and this data allowed managers to dig deeper to find the reason. This kind of granular insight into overall system function allows managers to increase capacity without adding to their labor pool or increasing the warehouse footprint.
The Yonder dashboard allows managers at all levels to break down the data collected in whatever way they need to isolate specific parts of the operation and analyze productivity. This tool gives additional insight into an overall operation that reaches far beyond the tasks they’ve chosen to automate, and its capabilities will continue to expand in our beta Yonder Analytics Program.
Join the Beta Program!
Plus One is looking for a few more companies interested in gaining performance insight to take part in our beta Yonder Analytics program. To apply, call (210) 664-3200 x124 or email info@plusonerobotics.com today!
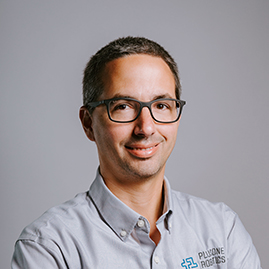
Shaun Edwards
Shaun Edwards is the CTO and Co-Founder at Plus One Robotics. Shaun's role at Plus One includes forming the company's technical vision, interfacing with customers, creating product roadmaps, and software architecture.