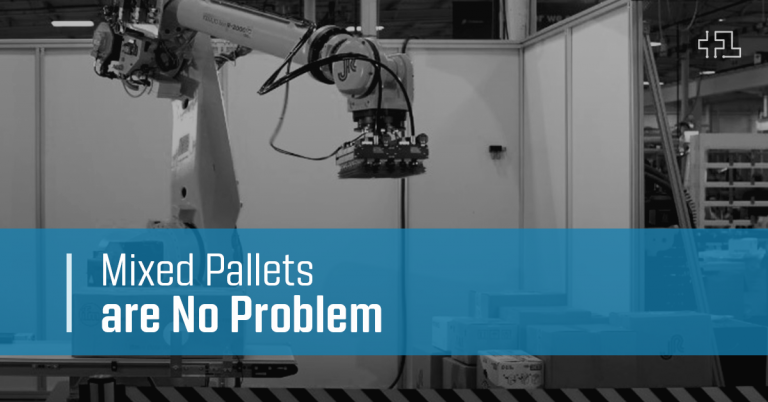
PickOne and Yonder Software are Setting High Expectations for Depalletization as eCommerce Booms
I spent years learning about the needs and dynamics of warehouse automation at companies like Dematic and Southwest Research. During those years, I had the opportunity to work with the Plus One Robotics founders and CEO. I realized that we shared a passion for getting robotic technology into the logistics space to make the human aspects of this work more enjoyable.
Elevating Humans As Robots Work
Empowering robots to do work that has historically required a human’s decision-making capability isn’t easy. There are so many complicated questions in the logistics of a warehouse supply chain, and most of the answers fall into the realm of moving more products as efficiently and as quickly as possible without the need for intervention. One of the most difficult problems to solve in this space has been mixed depalletization.
As e-commerce grows and unique items (SKUs - stock-keeping units) proliferate, increasing customer demand requires logistics centers to handle daily shipments that change constantly, and these logistics centers cannot always predict the contents of a shipment. Where warehouses once received single-item shipments with a known pallet pattern that a basic robotic arm could handle, today they’re bringing in pallets containing diverse products and they need to move them faster than ever.
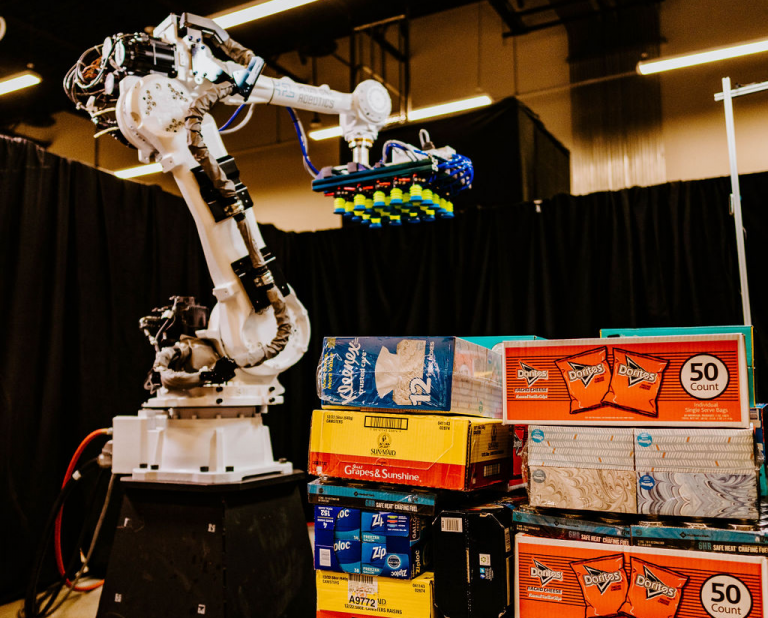
The Mixed Case Conundrum
A mixed case pallet will contain items of different sizes and different kinds of packaging. There might be boxes, cans, bottles, and bags, and they’ll make up an array of non-uniform layers and heights. And then there are other packaging issues like highly reflective packaging that makes it tough for vision software to get a clear image and decide where to pick an item. A bad pick can result in a dropped item or a bad place. And that equates to bigger problems down the line or can result in work stoppage and require intervention. In the high-capacity environments these robots operate within, even a one-percent deficit can significantly impact throughput.
These are easy problems for human workers to solve. A human can look at a group of items and decide how to handle each one--where to pick it up, how to hold it, how to place it on the conveyor--without much conscious thought. But we all know the work isn’t cognitively satisfying, and the repetitive motion of unloading pallets can wear on humans over time, resulting in high turnover and low employee engagement. Plus One’s vision and AI software, PickOne, can also accurately evaluate the best pick pose in most situations, but when the odd angles that naturally result from transport or some kind of novel packaging cause low confidence, things change.
This is where even excellent AI-driven vision software needs help, and this is where Plus One shines. PickOne signals a human Crew Chief to provide help with the exception, and that help comes remotely and immediately through Yonder, our remote supervisor software. This keeps the human in the loop but elevates them so their job requires high-level decision making instead of rote manual labor, and a happy side result is lower staff turnover and higher job satisfaction.
What makes the Plus One Robotics solution different from other AI-driven software powering robots? A few things, actually.
The human in the loop is the obvious thing. The Yonder software thresholds can be customized based on the kinds of things coming in so that the software signals the human Crew Chief when it isn’t sure what it’s seeing. The human can indicate the proper pick points from a remote location, the robot gets back to work, and the AI is programmed to handle that exception the next time. One client implementation began at a pick accuracy rate around 85% out of the box and had increased that rate to 94% in three weeks and 98% in six weeks. They used Yonder to collect data about the new and unusual items the robot was seeing and managed those exceptions in their product set without the robot ever stopping. Downtime is cut and throughput is maintained.
But there are a few other unique attributes that make me excited to talk about the way Plus One is handling the complexities of the mixed pallet.
- Our software can handle pallets up to eight feet high, with the sensor still able to accurately account for even tiny objects on that bottom layer. Of course, our sensors work equally well with standard five and six-foot pallets too.
- Yonder and PickOne can easily handle slip sheets, the smooth paper or plastic sheet often placed between layers on a pallet to help things stack more securely and prevent splaying outward of layers. Some software will see this large smooth item as a single large box, others will stop altogether, reporting very low confidence. But Plus One’s solution can handle slip sheets automatically or with a Yonder review, keeping things moving.
- The software also gives the robot the ability to pick multiple products in one pick motion dynamically. Most of the time, depending on the size of the gripper, an average product set is used to pick one or two items. In a set of products where the product is smaller than the gripper, it might pick up four or five at a time. The beauty of the software is that it evaluates the scene independently and chooses how many products to pick based on what it sees. If the warehouse can singulate products downstream, this is a huge boost in maximizing throughput, but if they cannot singulate, it can still be a time saver. The robot can be instructed to pick up products in a front-to-back orientation allowing the packages to separate naturally as they go through the conveyor system, adjusting on the fly and even picking up and replacing items when it recognizes something that will cause an issue downstream.
I’m excited about the innovations that Plus One’s software has brought to handling the increasing diversity within the logistics space, but I’m even more excited about what’s coming next.
A variety of new tools are arriving, which allow for innovative ways to apply technology taking advantage of mobility automation and analytics advances, and approach the even more complex issues that occur between the inbound and outbound portions of the logistics space. The inner workings of the warehouse are changing, and the future of Plus One Robotics is leading us right into the thick of it. I can’t wait!
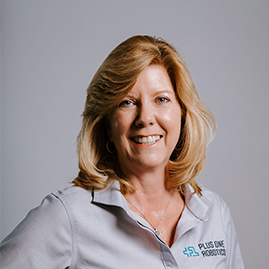
Crystal Parrott
Crystal Parrot is the Vice President of Engineering at Plus One Robotics. With more than 30 years in the robotics and automation industries, Crystal Parrott has a history of bringing emerging technologies to market. Crystal holds a Master of Science in Management of Technology from the University of Texas at San Antonio as well as a Bachelor of Science in Electrical Engineering from Kettering University.